Project
South Quay Plaza
Known as Hampton Tower, the South Quay Plaza development comprises 3 residential towers, the largest of which is one of Europe’s tallest residential buildings.
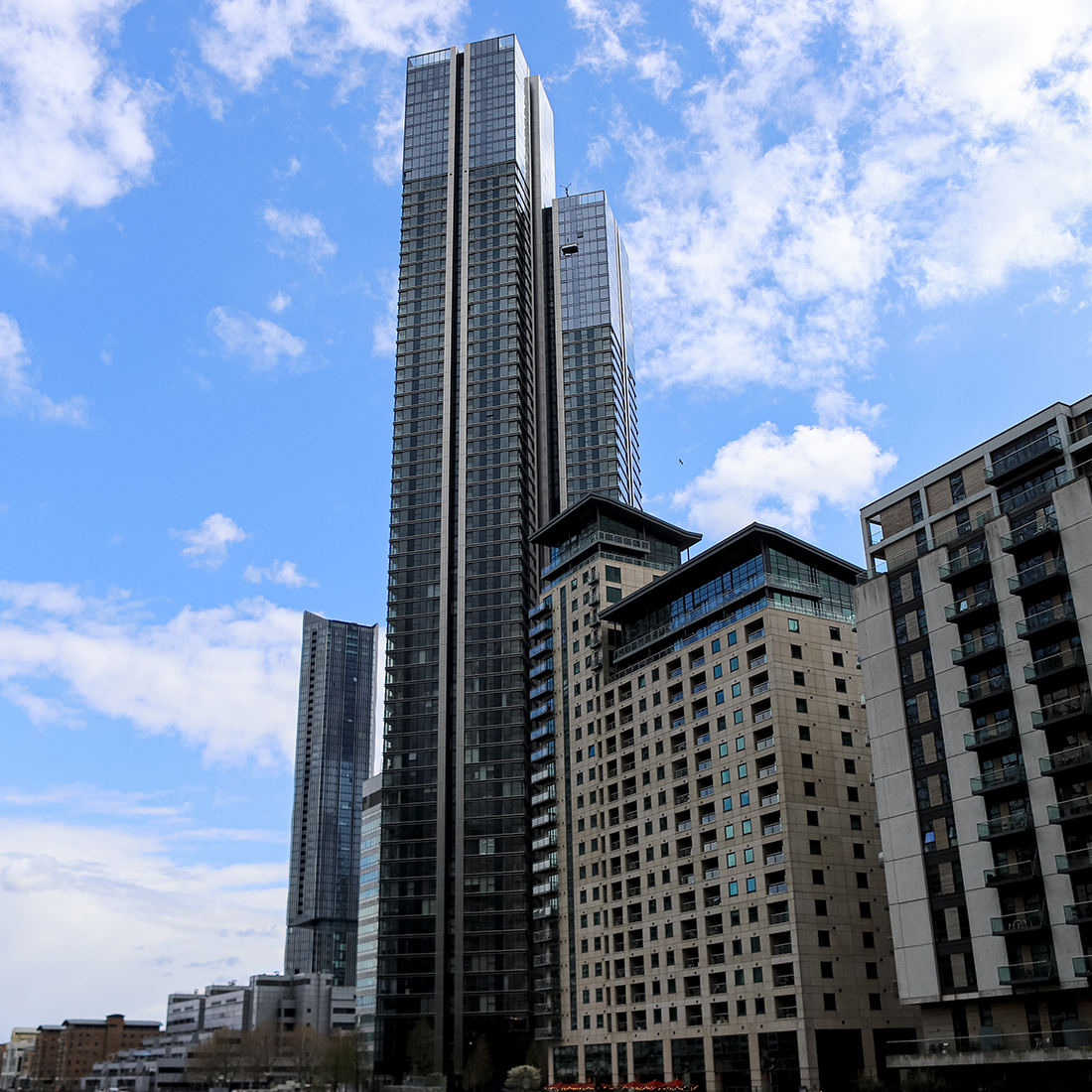
Summary
Project
South Quay Plaza
Main Contractor
Berkeley Group
M&E Consultant
WSP
Fire Resisting Value
£3.1m
Project description
Known as Hampton Tower, the South Quay Plaza development comprises 3 residential towers, the largest of which is one of Europe’s tallest residential buildings, standing at 68 storeys high. This brought its own challenges with regards to maintaining productivity to achieve programme dates, due to the logistical issues of moving labour and materials over 68 storeys.
The design for development saw the exhaust for the basement smoke extract system being discharged out of the building via a number of large soffit-mounted plenums, some of which exceed 30m in length, fixed to the underside of the basement soffit.
The complex provides 5* facilities, including a 20-metre pool, a state-of-the-art gymnasium, health club & spa, and boasts a residential bar and terrace on the 56th floor - one of the highest in Europe.
Scope
Fire Protection was responsible for supplying and installing both the fire-resisting and GSS ductwork for this project, along with the procurement and installation of fans, silencers, grilles and complete smoke damper package.
The fire resisting ductwork package was made up of a large basement smoke extract and make-up air system, including bespoke ceiling plenums in excess of 30m x 20m.
We also supplied and installed 3 firefighting lobby smoke extract systems serving all 68 levels of the building.
Project highlights
One of the biggest challenges we faced was to maintain productivity over the 68 floors in order to ensure we met the client’s compacted programme. We achieved this by using the main goods lift to move 10 floors of ductwork at a time, and then distributing the ductwork throughout the floors above and below. This meant that labour and materials were not waiting around to use the extremely busy lift.
The largest challenge was the installation of the soffit-mounted plenums, due to their size and the restraints on transporting them to site and lifting them into position. We overcame this by manufacturing 2m x 1m rectangular plates with angle frames along each edge.These were then constructed in situ within the basement, which allowed for the final site measurements of bespoke panel sections around the columns.
Contact
Ready to work
together?
Get in touch with our fully trained and experienced team to discuss the manufacture and installation of our passive fire resisting systems, and how these third party accredited systems can be implemented within your project.