Project
Bond Street Crossrail
Bond Street Station is comprised of many different systems serving different purposes. These vary from the main smoke extraction system on the platforms on level -5, through to the two pressurisation systems.
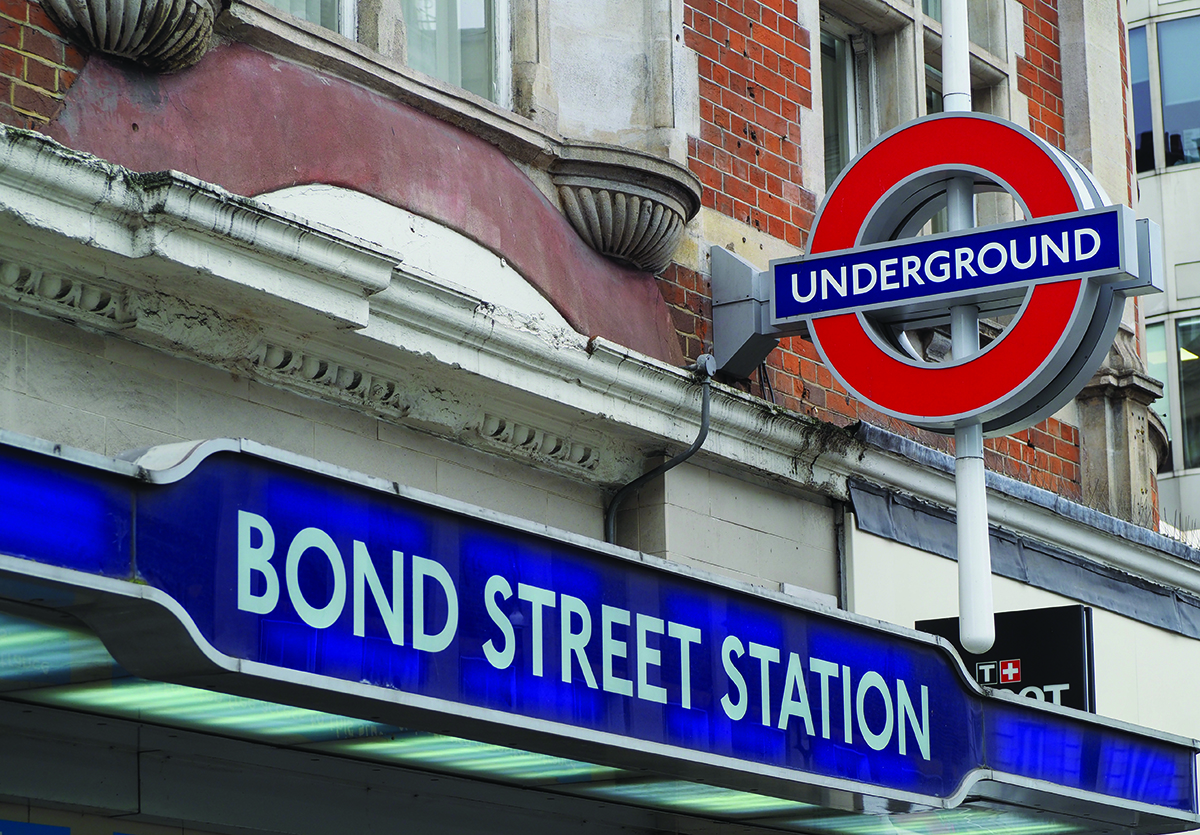
Summary
Project
Bond Street Crossrail
Main Contractor
Costain, Skanska, Joint Venture
M&E Consultant
Arup
Fire Resisting Value
£5.2m
Products used
Project description
Bond Street Crossrail is unique from a lot of other projects because of the access requirements for the majority of rooms. Like any project, works are planned out well in advance of commencing. However, as the rooms are energised by the client, we are required to complete various on-site training courses in order to work in them. These vary from low-voltage competent person training, to accessing high voltage rooms. The latest challenge was a course to allow us to access RFLi rooms, which are all areas under Transport for London control as they run hourly test trains through the station. Such requirements present a unique set of challenges to overcome.
Because of the initial design and consequent design changes, there is a large volume of removing works to carry out in order for other trades to complete their works.We are therefore on a site where we have to balance working efficiently with moving materials, so as to not block work faces for other trades.
Scope
Bond Street Station is comprised of many different systems serving different purposes. These vary from the main smoke extraction system on the platforms on level -5, through to the two pressurisation systems, to ensure there is always a positive pressure in the escape stairwells from the platform, whilst maintaining a negative pressure in the lobbies on each level to prevent smoke egress into the more critical areas.
There is also a variety of other systems, from ancillary supply and extract, to plant room supplies and extraction systems, all of which connect to the externals of the building through their own plenums. The largest of these measures at 9.6m wide by 2.3m high by 1.2m deep.
Project highlights
As mentioned above, accessing many of the rooms on site can be one of the biggest challenges. It means ensuring our 4-week plans are constant and up to date, to allow for access documents to be submitted early before works can take place. Any underground project poses its own challenges, particularly as contacting one another on site becomes an issue when mobile phones are just not an option. To overcome issues of communication, we use two-way radios.
Finally, the biggest challenge of all has been the installation surrounding fire stopping compartmentation. Because the original contractors who performed the fire stopping installation did a poor job, lintels have been retrofitted, by necessity, through the majority of walls. This means we have had to adapt our installation routes to suit, setting before and after most wall-lines.
Contact
Ready to work
together?
Get in touch with our fully trained and experienced team to discuss the manufacture and installation of our passive fire resisting systems, and how these third party accredited systems can be implemented within your project.